工程塑料的切削性能研究
时间:2005-07-05
1 引言
由于非金属材料具有一些优于金属材料的独特性能,所以在我国现代化建设特别是高新技术产业中发挥着越来越重要的作用,其应用领域与应用数量均以较高的速度不断扩大。工程塑料是发展最快、应用最广的材料之一,工程塑料密度小,耐酸、碱及有机溶剂腐蚀,具有良好的绝缘性、耐磨性、减震性和自润性,可用于许多金属和其他非金属材料所不能胜任的应用场合。随着科学技术的发展,预计今后工程塑料在工程材料中所占的比例会越来越大。工程塑料制品的制造除了直接成型以外,对某些几何形状、尺寸精度和表面加工质量要求较高的工程塑料制品,往往需要进行切削加工。由于工程塑料的物理、机械性能与金属材料的物理、机械性能有着较大的差异,所以工程塑料的切削机理与金属材料的切削机理有较大的不同,这样就使得切削参数、刀具材料等的选择原则也有较大的区别。本文通过分析工程塑料的性能对其切削加工性的影响及切削参数对工件加工质量和刀具耐用度的影响,提出了切削参数合理选择的原则。
2 工程塑料的性能对切削加工的影响
热性能的影响
工程塑料的导热系数很低,一般仅为金属的1/175~1/450,因此切削过程中的散热条件很差,刀具与工件之间由于摩擦所产生的热量通过工件传递走的比例较少,致使切削区形成局部高温导致刀具发生塑性破损、刃口变钝。工程塑料的热膨胀系数大(一般比金属大1.5~2倍),切削区的局部高温将使被加工零件的体积膨胀导致其尺寸精度及形状精度下降,同时零件的体积膨胀加剧了刀具与被加工零件之间摩擦热的产生,引起切削温度的进一步增高,导致工件因过热而烧焦或熔化造成废品。为了避免上述情况,应采用导热系数较高的刀具材料,提高从刀具中传走的切削热的比例,或者在加工过程中采用冷却剂(常用的冷却剂有压缩空气等)。
弹性模量的影响
一些工程塑料的弹性模量较高,当切削力较大时,刀具沿工件表面走过后工件将产生回弹,造成工件变形,导致尺寸精度及位置精度下降。为避免这种情况,应采用较锋利的刀具并以较小的切削深度进行切削。
脆性的影响
工程塑料可分为热塑性和热固性两大类:热固性塑料由加热固化的合成树脂所制成,固化后的塑料质地坚硬,加热后不能使它软化也不具有可塑性;热塑性材料由经多次反复加热仍具有可塑性的合成树脂制成,这种材料遇热后即软化或熔化,冷却时又凝固坚硬。
因此,在切削热固性工程塑料时,其切削过程与切削脆性金属类似,切屑变形时不存在塑性变形区,形成的切屑为高速脱落的崩碎切屑。在刀具切入切出时工件表面会出现崩落现象。切削力或刀尖圆弧半径较大时工件易开裂,工件表面出现银丝裂纹。因此,在加工脆性较大的热固性工程塑料时,应选择较锋利的刀具。在切削热塑性工程塑料时,由于摩擦导致工件发热,使其具有一定的塑性,从而形成带状切屑,其切削过程与切削塑性金属类似。由于热固性塑料比热塑性塑料加工难度大,所以本文重点分析热固性工程塑料的切削加工性能及切削参数的合理选择。
3 切削参数的合理选择
实际生产中提高加工质量、降低加工成本或提高生产率三者之间往往是彼此矛盾的。当工件材料、刀具、机床都确定后,切削参数(即切削速度、进给量、切削深度)的合理选取对提高生产效率、降低生产成本、保证零件的加工质量及必要的刀具耐用度具有重要的意义。
1) 切削速度
在切削工程塑料时,提高切削速度可以缩短切削时间、提高劳动生产率,且切削力变化不大,但切削速度的增加会使刀具后刀面与已加工表面之间的摩擦加剧,单位时间内的摩擦功和弹性变形功也增大,导致切削热增加。由于工件的导热系数低、散热条件差,切削热的增加会使切削区的温度急剧升高,导致工件表面烧焦或分解;同时由于工程塑料的热膨胀系数较高将使工件产生热变形。这样将造成工件的加工精度与加工质量下降,同时刀尖会因无法承受切削高温而发生烧蚀或急剧磨损。
实验证明,当切削速度在某一范围内时,切削速度对工件表面粗糙度也有一定的影响。图1为加工不同的工件材料时工件表面粗糙度Ra与切削速度v之间的关系曲线图。从图中可以看出,在低速范围内随着切削速度的增加工件表面粗糙度下降较明显,在v≈45~50m/min时,表面粗糙度Ra达到最小值,之后随着v的增加Ra也增大;而当高速切削(v>100~150m/min)时,切削速度对表面粗糙度Ra的影响比较小。
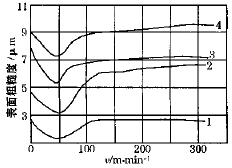
1.有机玻璃 2.纤维塑料
3.增强纤维塑料 4.织物布层压塑料
图1 加工表面粗糙度与切削速度的关系
从上述分析可以看出,高速切削对工件加工质量与刀具耐用度的影响很大,但对表面粗糙度和切削力的影响较小。为了提高劳动生产率、降低生产成本、保证必要的加工质量与刀具耐用度,加工不同的工程塑料时需采用不同的刀具材料。高速切削工程塑料时,应采用导热系数较高的刀具材料,目前常用的刀具材料有高速钢、硬质合金、金刚石、陶瓷等。聚晶金刚石(PCD)材料具有高导热系数、高硬度、高耐磨性及低摩擦系数,适用于工程塑料的高速切削。陶瓷材料虽然具有优良的耐磨性、耐热性等,但脆性大、导热系数低,使用上受到一定的限制。
使用不同的刀具材料切削各种工程塑料时,可按下式计算最佳切削速度:
式中
| CV——刀具材料修正系数 T——刀具耐用度(min) ap——切削深度(mm) f——进给量(mm/r) X、Y、Z——分别为刀具耐用度、切削深度、进给量修正指数 KT、KW——分别为耐用度修正系数、加工类型修正系数 |
2) 进给量和切削深度
进给量和切削深度的增加不仅可以缩短切削时间、提高劳动生产率,而且增加了切削层面积和散热体积,从而改善了切削区的散热条件,所以进给量和切削深度的增加对切削温度的影响不大。同时,实验证明,当进给量和切削深度的取值范围不同时,刀具磨损量也不同。图2、图3分别为用硬质合金刀具加工工程塑料时进给量和切削深度对刀具磨损的影响曲线图。从图2可以看出,当进给量f>0.41mm/r时刀具磨损量较大,当f<0.41mm/r时,随着进给量的增加刀具磨损量减少。因此,粗加工时为了提高劳动生产率及保证一定的刀具耐用度,可取较大的进给量。另一方面,进给量增加也会使工件表面残留面积增大,造成表面粗糙度Ra值增加,同时由于切削层面积的增加,切削力也会明显增加,所以精加工时一般应取较小的进给量。
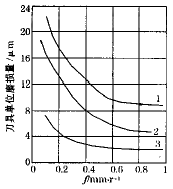
1.玻璃纤维(v=150m/min)
2.酚醛(v=300m/min)
3.石棉层压塑料(v=500m/min)
图2 进给量对刀具磨损的影响
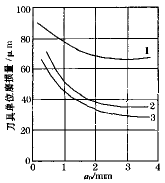
1.石棉层压塑料(v=300m/min)
2.织物布层压塑料(v=400m/min)
3.酚醛(v=150m/min)
图3 切削深度对刀具磨损的影响
从图3可以看出,当切削深度较小(ap<1.5mm)时,刀具磨损量较大,而当ap>2mm时,刀具磨损量几乎不随切削深度的增加而变化。但并非可以无限制地增大切削深度,因为在切削工程塑料时,切削深度对切削力影响最大,由于工程塑料的弹性模量较大,当切削力较大时,刀具走过后工件会产生回弹,造成工件变形而影响加工质量。因此,在实际生产中要根据不同的工件材料和加工要求合理选择切削深度。
采用硬质合金刀具加工各种热固性工程塑料时的切削参数推荐值见表1。
表1 热固性工程塑料的切削参数
工件材料
| 切削速度(m/min)
| 进给量(mm/r)
| 切削深度(mm)
|
粗加工
| 精加工
| 粗加工
| 精加工
| 粗加工
| 精加工
|
酚醛
| 80-160
| 150-300
| 0.2-0.35
| 0.1-0.2
| 2.0-3.0
| 0.5-2.0
|
酚基塑料
| 400-500
| 600-800
| 0.1-0.3
| 0.05-0.1
| 1.5-3.0
| 0.5-1.5
|
氨基塑料
| 200-450
| 500-600
| 0.08-0.25
| 0.05-0.1
| 1.5-3.0
| 0.5-1.0
|
纤维塑料
| 300-450
| 500-600
| 0.1-0.2
| 0.05-0.1
| 3.0-5.0
| 1.0-2.5
|
织物布层压塑料
| 90-180
| 300-800
| 0.1-0.5
| 0.08-0.2
| 3.0-5.0
| 0.5-1.5
|
玻璃布层压塑料
| 90-100
| 120-160
| 0.1-0.2
| 0.06-0.10
| 2.0-3.5
| 0.5-2.0 |
4 结论
在切削工程塑料时,切削速度对工件加工质量和刀具耐用度影响最大。高速切削工程塑料时,由于材料导热系数低、散热条件差,为避免切削温度急剧升高影响工件的加工质量和刀具耐用度,应采用导热系数较高的刀具材料同时采用冷却剂(如压缩空气)进行冷却。
进给量和切削深度对切削温度的影响较小。随着进给量和切削深度的增加刀具耐用度将有所增加。切削深度对切削力影响最大,由于工程塑料的弹性模量较大,当切削力较大时,加工后工件会产生回弹,造成工件变形而影响加工质量。因此,应根据不同的工件材料和加工要求合理选择切削深度。