汽车用碳纤维复合摩阻材料的摩擦磨损特性研究
时间:2005-07-05
摘要:
研究了汽车用碳纤维复合摩阻材料在实际工况下的摩擦磨损特性,分析了碳纤维含量及碳纤维的强度、表面状态等对磨损机制的影响。实验研究结果表明,碳纤维复合摩阻材料的磨损性能、工作寿命与抗热衰退性能均明显高于传统的石棉摩阻材料。
前言
用传统的石棉摩阻材料制成的汽车制动器衬片,不但污染环境有致癌作用,而且工作寿命低,其在250℃以上工作时有热衰退现象。因此,近二十年来世界各国都对石棉摩阻材料的生产与使用加以限制,并致力于研究新一代摩阻材料来取代石棉摩阻材料。本研究工作在采用正交设计优化了碳纤维复合摩阻材料的基础上,针对汽车制动器衬片的实际工况,研究了碳纤维复合摩阻材料的摩擦磨损特性及磨损机制。本研究结果为研制碳纤维复合材料汽车用制动衬片打下了基础。
1 实验材料、内容及方法
1.1 实验材料的成分设计与制备
实验材料系用碳纤维作增强纤维,改性酚醛树脂作粘接剂并辅有各种性能调节剂与填料的多元组分体系。在材料成分配方设计中,采用了L16(45)正交优化设计方法,并经多轮实验后,确定了碳纤维复合摩阻材料的经济实用型配方(见表1):
表1 实验用碳纤维复合摩阻材料的成分
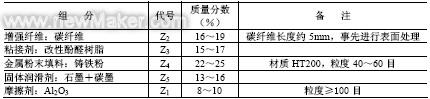
注:碳纤维分别选用吉林炭素厂与辽源市碳纤维厂生产的高碳纤维、低碳纤维与预氧纤维,并按不同强度的碳纤维组分进行实验。
按上述配方(其中碳纤维的强度不同),将各组分经过均匀混料、干燥处理后,用热模压成型压制成碳纤维复合材料汽车制动衬片试样[2]。
1.2 摩擦磨损实验
在MM-200 磨损实验机上进行磨损实验,实验参数为:
摩擦压力F=200kN
转速n=400 rad/s
摩擦配副为直径φ40mm,材质为HT400 的磨轮。
采用感量万分之一的精密天平称量试样的磨损量。在JSM-5310 型扫描电子显微镜上观察磨损面的表面形貌。
磨损实验结果处理后的数据见表2:
表2 磨损实验结果处理
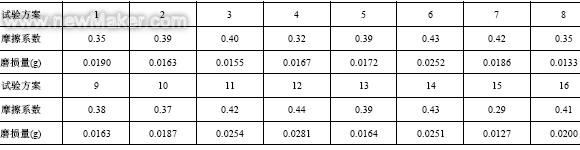
图1 与图2 为碳纤维表面经过改性处理与未经改性处理的SEM 照片。

图1 经表面处理的碳纤维摩阻材料的SEM 照片 图2 未经表面处理的碳纤维摩阻材料的SEM 照片
1.3 在D-MS 实验机上进行热衰退实验
在300℃实验温度条件下,分别按摩擦系数和磨损率进行实验分析各组分的影响次序。实验结果见表3。
表3 碳纤维不同表面状态时的热衰退实验结果
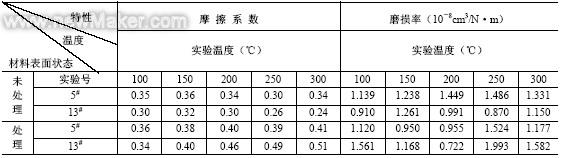
2 实验结果与分析
2.1 碳纤维对摩阻材料摩擦磨损特性的影响
2.1.1 碳纤维含量对摩擦磨损特性的影响
碳纤维含量是影响本摩阻材料摩擦磨损性能的重要因素。实验结果表明:当碳纤维含量较低时(15%~19%)摩擦系数与磨损率随碳纤维含量的增加而减少;而当碳纤维含量较高(19%~25%)时摩擦系数与磨损率都随着碳纤维含量的增加而增大。
出现第一种现象是因为碳纤维属“乱层石墨”式结构,其本身具有良好的自润滑性能,能起一定的减摩作用,致使摩擦系数减小[5]。在滑摩时,发生在摩擦界面上因碳纤维引起的犁削阻力较小,故此时碳纤维的减摩作用明显,因而会呈现随碳纤维含量增加摩擦系数与磨损率随之减小的现象。
出现第二种现象是因为当碳纤维含量相当高时,由于碳纤维比强度、比模量很高,故滑摩时的犁削阻力相当大,远远超过了碳纤维的减摩作用,从而呈现出摩擦系数随碳纤维含量的增加而增大的现象。同时,当犁削阻力大于碳纤维机体的结合强度时就会发生磨损,故随着碳纤维含量的继续增加,磨损率也会增大。
2.1.2 碳纤维表面状态对摩擦磨损特性的影响
对碳纤维需进行表面处理,以达到强化与粘接剂改性酚醛树脂的润湿与粘接的目的。
将对碳纤维进行表面改性处理的与未经处理的试样进行对比实验。碳纤维进行表面改性处理的工艺是:将碳纤维置于50%的硝酸水溶液中处理24h 后取出,用水冲洗干净并作干燥处理后,再进行混料。
碳纤维与基体的粘接力在很大程度上取决于其表面性质。未经表面改性处理的碳纤维,由于其表面惰性,与粘接剂的相溶性差,致使摩阻材料的抗剪强度低,当对碳纤维进行表面改性处理后,会使其表面的沉积物减小,表面粗糙度增大,进而提高强度并增大摩擦系数,有利于提高锚固作用。图3 与图4 为碳纤维表面经改性处理与未经改性处理的摩擦材料的摩擦系数和磨损率对比。
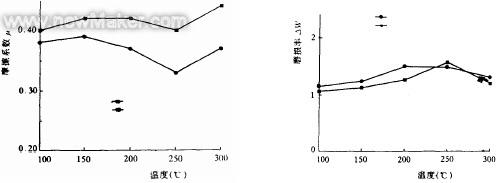
图3 碳纤维不同表示形态时的摩阻材料的摩擦系数 图4 碳纤维不同表示形态时的摩阻材料的摩损率
经过改性处理的碳纤维与基体结合好而紧密。这是因为经处理后碳纤维表面含氧官能团增多,提高了碳纤维与粘接剂的反应性,因而碳纤维自身的浸溶性提高,也增加了碳纤维与粘接剂的结合强度。因此,经改性处理后的碳纤维复合摩阻材料表面现出较好的摩擦磨损性能。图5 是用23%的碳纤维所制成的制动衬片的温度与摩擦系数,时间与摩擦系数的关系。
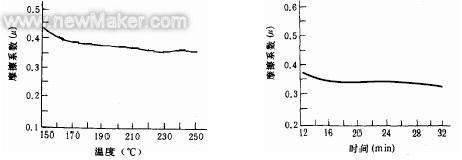
图5 摩擦系数与温度和时间的关系
2.1.3 碳纤维强度对摩擦磨损性能的影响
实验结果表明碳纤维强度越大,用其增强的摩阻材料的磨损系数也越大。这是因为碳纤维的比强度和比模量越高,摩擦时抗犁削阻力就越大,因此摩擦系数也越高。
2.2 碳纤维对摩阻材料抗热衰退性的影响
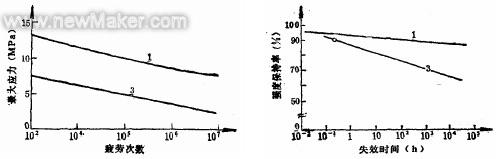
图6 碳纤维的疲劳特性 图7 碳纤维的蠕变特性
碳纤维复合摩阻材料具有较高的强度( sb =17MPa, t = 90MPa),弹性模量(125GPa),故其具有较高的疲劳特性、蠕变特性(图6、图7)[1]。此外它还因碳纤维具有良好的导热性,高温性能好,故在高温条件下能减小犁削深度并减小材料表面层的剥落,抵御磨料运动的能力增强。所以碳纤维复合摩阻材料的抗热衰退性能好,明显优于石棉摩阻材料与半金属摩阻材料。在D-MS 实验机上将碳纤维复合材料制动器衬片与日本产的半金属制动器衬片和国产石棉制动器衬片进行的对比实验结果见表4。
表4 三种制动器衬片摩擦磨损性能对比实验结果

经在中科学院长春应用化学研究所进行热重分析(TAG),测定摩阻材料不同深度表面层中有机组分的含量,进而求出热影响表面层的深度。测定结果为:碳纤维摩阻材料的热影响表面层深度小于0.55mm,石棉摩阻材料为0.75mm,这证明了由于碳纤维导热率高,会使材料内场的温度梯度下降,热分解层薄,因而碳纤维摩阻材料在很高的温度时摩擦磨损性能很稳定,提高了工作性能和抗热衰退性能。其主要性能指标达到了GB5736-1998《汽车用制动器衬片》的标准值:
摩擦温度 100℃ 250℃ 300℃
摩擦系数 0.42±0.06 0.42±0.09 0.42±0.1
磨损率 ≤0.10 ≤0.41 ≤0.60
2.3 碳纤维复合材料的磨损特性与磨损机理
2.3.1 碳纤维复合摩阻材料的摩擦磨损特性
由于碳纤维具有很高的强度和弹性模量,并且具有很好的耐蠕变性、导热性,将其进行表面改性处理后,以较高的组分制成的碳纤维复合摩阻材料具有良好的摩擦磨损特性。
在工作温度低于250℃时,碳纤维复合摩阻材料的摩擦系数较高,且稳定在0.32~0.44 之间,在此温度范围之内磨损率变化也很小。
在滑摩速度为0.6m/s,载荷为200kN 时,碳纤维复合摩阻材料的磨损特性相当稳定,且回复性好,抗热衰退性能好,基本上不发生蠕变。
2.3.2 碳纤维复合摩阻材料的磨损机理
在工作状态下,碳纤维复合摩阻材料制成的制动衬片与制动盘滑摩时,摩阻材料的磨损与比压和滑摩速度成正比。在工作过程中,其接触压和磨损是在内外侧交替进行的,最终会使摩擦衬片沿径向的磨损保持均匀。在制动时,第一阶段因滑动速度较高在摩阻材料表面的磨损机制主要是犁削磨损。随着制动过程的进行,第二阶段磨损除了犁削磨损外还有粘着磨损,磨屑中有显微切屑与片状剥落。由于碳纤维复合摩阻材料表面层强度高,耐疲劳性好,故能有效地抵御制动盘的磨料压入,而使犁削深度和表层材料的转移磨失体积减小。在温度升高时,由于碳纤维自身具有强度高、导热性与减摩性能好,故能有效地降低粘着磨损,减少剥离磨损。在反复制动的动态接触中,因其磨损系统呈现“衬片均匀磨损”特征,再加之碳素纤维具有良好的导热性和耐蠕变性,故碳素纤维复合磨阻材料具有较高的摩擦磨损性能。
3 结论
目前国内外对开发新型摩阻材料及对其磨损机理的研究已进行了大量的工作。但因碳纤维复合摩阻材料是一种新型复合材料,其工作过程的磨损是涉及到摩擦系统的外部条件和材料组成因素的复杂的物理—化学过程,对其摩擦学性能的研究大多都局限于一定的试验条件或以经验为依据。有关其磨损机理的研究和磨损模型的建立还有待于继续深入与完善,本文主要结合轿车盘式制动器摩擦块的国产化,采用碳纤维作增强纤维,通过系统试验分析,得出了碳纤维复合摩阻材料的磨损特性及其优点如下:
1)碳纤维复合摩阻材料是性能优异的新一代摩阻材料,其摩擦系数较高,抗热衰退性能好,工作寿命是石棉摩阻材料的2~3 倍。
2)碳纤维的组分与表面状态、强度对碳纤维复合摩阻材料的摩擦磨损性能有显著的影响,本研究中通过优化碳纤维含量(19%~25%),选用高强度并经表面改性处理的碳纤维设计的复合摩阻材料,具有较高的摩擦磨损性能。实际应用时,呈现出摩擦平稳和良好的制动性能。
3)碳纤维复合摩阻材料的磨损机制主要是犁削磨损和粘着磨损 。由高强度、耐疲劳、导热性好且具有减摩作用的碳纤维组分制成的复合摩阻材料能减小犁削深度,降低粘着磨损。