搜索:
热塑性树脂基体纤维缠绕工艺
时间:2005-07-02
热塑性树脂及其复合材料近十多年来得到了迅速发展。与热固性材料相比,热塑性树脂具有优异的抗冲击韧性、耐疲劳损伤性能、成型周期短、生产效率高、可长期贮存、可进行修补和回收再利用等一系列优点。因而在航空航天、医疗、电子、机械等领域得到了越来越广泛的发展和应用。特别是随着刚性、耐热性及耐介质性好的的新型芳族热塑性树脂基复合材料的出现,使得热塑性复合材料克服了以往弹性模量低、抗溶剂性差、纤维与树脂结合强度低等缺点,可用于性能要求较高的结构材料。
航空航天中常用的热固性树脂常温下一般为液体,常温加工即可,相比而言高性能热塑性复合材料成型时一般需要较高的温度。常用的热固性树脂的固化温度为250°以下,而PEEK等热测性复合材料成型温度在350℃以上。同时先进热塑性复合材料的成型压力较大,而热固性复合材料的成用压力很低。较高的成型温度和较大的成型压力使得先进热塑性复合材料的制造成本很高,这是目前它们在各行业上的应用尚不普遍的根本原因之一。常用的热塑性复合材料成型工艺有:模压成型、热压罐成型、隔膜成型、拉挤成型、压延成型、纤维缠绕成型等,其中缠绕技术能较好的实现低成本和高效率的结合。热塑性树脂纤维缠绕既可像多数热固性系统所用的方式那样,先将热塑性预浸带用于法缠绕成型,然后在固化炉或热压罐内固化;又可用就地固化工艺成型。所谓就地固化成型就是利用热塑性树脂可再熔融的特点,缠绕时加热使材料粘结就位,并尽可能除掉残留的事气,同化所需压力由压力辊在接触部位提供,缠绕完冷却即获得终产品,不需再进行后固化。这种成型工艺最大的优点就是省去了热固性树脂复合材料成型的后固化过程,简化了生产流程,降低了生产成本,并打破了固化环节带来的一些对产品规格、性能的限制。
2 研究状况
热塑性树脂基体纤维缠绕工艺包括预浸带的成型,缠绕过程的加热、加压方式等诸多过程和因素,以下分别阐述:
2.1 新型高性能树脂基体
目前的高性能热塑性树脂主要有聚醚醚酮(PEEK)、聚苯硫酸(PPS)、聚醚酰亚胺(PEI)、聚醚砜(PES)、聚酰胺(PA)和聚酰胺酰亚胺(PAI)、聚酸亚胺(PI)等,其中很多已经工业化生产。下表列出了一些主要产品的性能及生产厂家。
缩写及牌号 |
Tg/℃ |
Tm/℃ |
成型温度/℃ |
拉伸强度/MPa |
拉伸模量/MPa |
生产厂家 |
PEEK |
143 |
343 |
400 |
100 |
3103 |
ICI |
PEK |
165 |
365 |
400-450 |
110 |
4000 |
BASF |
PEKK |
156 |
338 |
380 |
102 |
4500 |
Du Pont |
PAK(PXM8505) |
265 |
|
- |
88 |
2482 |
Amoco |
PPS(Ryton) |
90 |
290 |
343 |
83 |
4344 |
Phillips Pet |
PAS(PAS-2) |
215 |
|
329 |
100 |
3241 |
Phillips Pet |
pa(J-1) |
145 |
279 |
343 |
69 |
2206 |
Du Pont |
PAI(Torlon) |
275 |
|
400 |
63 |
4599 |
Amoco |
PEI(P-IP) |
270 |
380 |
380-420 |
95 |
3000 |
Mitusi Toatsu |
PI(Avimidk-II) |
250-280 |
|
360 |
102 |
3690 |
Du Pont |
PES(VICTR EX4100G) |
230 |
|
300 |
84 |
2620 |
ICI |
2.2 热塑性预浸带的制备
悬浮法:将树脂粉末在机器或其他作用下分散于水中,形成悬浮液,然后经过类似于溶液法的工艺制势预浸料,这种方法已经用于制备PPS等难溶解的树脂预浸料,但由于悬浮液为热力学不稳定体系,有可能导致树脂分布不均匀。
薄膜镶嵌法:将热塑性树脂制成膜后与增强材料结合在一起,在成型过程中树脂熔融并浸渍纤维。这种组合体系需要较高的成型温度、压力,以保证良好的浸润及低的孔隙率。
溶液法:选取合适的溶剂并配成胶液,然后使纤维通过胶液得一浸渍,再烘干溶剂,便得到预浸带。这种方法虽然操作简便,但其树脂含量难以精确控制,而且残留的溶剂在最后成型时会引起材料发泡、表面缺陷及内部孔隙,制品性能不好控制。
静电粉末法:树脂粉末在流化室中经过压缩空气成流化状态,纤维通过流化室时,树脂自然沉积或由静电吸附与纤维结合。沉积了树脂的纤维在熔融炉和辊压设备作用下完成浸渍过程。
双纤维法:将带捻度的纤维制成外面包覆树脂层的双纤维,然后再加热压制成预浸带。
熔融浸渍法:纤维通过几个引导辊通过熔融的树脂槽得到浸渍。这种方法简便易行,效果也较好,是采用最普通的工艺。
资料反映目前对纤维预浸带制备工艺的研究正在向更高的纤维表面处理和更精确的浸胶量控制的方向发展。而一些重要的热塑性树脂在欧美国家已经实现了工业化产品生产,如:美国帝国化学公司/ICI生产的APC-2/AS4热塑性树脂/碳纤维预浸料带材等。
2.3 缠绕和后固化工艺
自从80年代末提出热塑性纤维复合材料缠绕工艺以来,国内外均对其进行了多方面的研究和生产实践。其中包括美国杜邦公司、帝国化学公司、德国凯瑟斯劳滕大学、BSAF公司等多家大公司和科研机构。研究内容涉及热塑性缠绕的设备、工艺过程、条件以及相关参数等。
大部分报道中热塑性缠绕工艺都被分为三个过程(如图1):
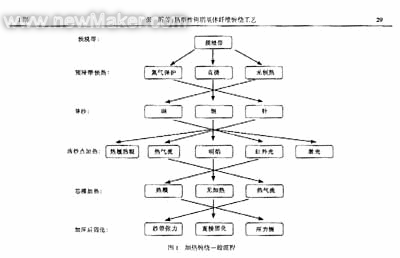
导纱(包括预浸带的预热):纤维预浸带由导辊引至缠绕芯模的过程。多数情况下配有一套导纱器来实施控制,有时为了加快缠绕速度,导纱过程中还要对预浸带进行预热。一些研究表明预热不仅对缠绕速度,缠绕张力等因素有影响,对提高制品的性能也很有利。一般的说来预热温度不小于树脂的Tg相关范围内得到的制品抗压强度比预热温度大于Tg的高(如PEEK)。
加热缠绕:加热缠绕是整个工艺的核心控制部分,其中加热方式的选择,缠绕速度、缠绕张力的调节,缠绕温度的控制对整个生产效益、产品性能等都有决定性作用。
常见的加热方式有:(1)气体对流加热,可选用空气、氮气等多种气体,优点是加热均匀,缺点是加热效率底、气体湍流损伤预浸带。(2)红外线加热,这种方法热效率高,加热时不用接触,是比较理想的热源。(3)激光加热,热效率极高,但费用昂贵且容易引起树脂降解。(4)微波加热,热容很大且不损伤纤维,应用的主要困难是设备复杂,成本高。(5)火焰加热,效率较高、设备简单,是一种常用的加热方式,缺点是容易造成局部过热使基体树脂降解。(6)热辊或芯模加热,通过热履或辊或直接由芯模加热,热效率效好,主要问题是辊加热会接触材料本身,造成了表面损伤;芯模加热则会限制制品的厚度。各种方法利弊不同,可视具体情况应用。现在大多 数的相关研究均采用复合加热方式,如:火焰加热与芯模加热相结合等。
对于缠绕速度,主要由以下几方面控制。(1)加热的效率要与速度匹配,速度太高导致预浸带上树脂末能充分受热熔融从而影响缠绕制品层间结合,速度太低则会导致预浸带过热变形甚至降解;(2)缠绕速度学要受到固化压力的限制。
缠绕过程的张力控制目前是研究的热点,有的文献中还报道省略了固化压力辊的缠绕装置,而其固化压力完全由缠绕张力提供。对于 不同的加热方式,缠绕张力的选择也有差异,以便最大限度的减小孔隙率。
缠绕温度方面的研究较少,一般控制在树脂基体熔点以上30℃-40℃左右,与纯树脂加工温度相差不大。值得注意的问题是,温度不能超过树脂降解温度,在高温区域加热时间不宜过长,避免树脂降解或农空气侵入造成树脂氧化。
加压冷却固化:热塑性纤维缠绕的固化有两种方法,一是采用压力履或辊在被缠绕部件的表面加太,另外就是对预浸带加张力并由此获得固化压力。为了消除制品的内应力,也有采用固化后处理方案,即将固化后的制品升温至接近基体熔 点,保温一段时间后冷却。这种方法能减少制品的内应力,但无法完全消除。
总体来说热塑性纤维缠绕工艺已发展到了一定阶段,但国内外研究进展差距很大,一些产品也已用于航空航天和发用。如:美国用CF/PEEK缠绕制件作飞机水平安定面,德国用CF/PA缠绕管制造超轻质自行车等。
3 展望
热塑性基体纤维缠绕工艺近些年来的发展表明,它具有优异的综合性能。国外一些机构甚至已开始对热塑性纤维缠绕的整个过程进行详细的热力学分析,利用若干热力学数学模型对缠绕过程进行大量的模拟和预测,对产品的孔隙状况和内应力进行计算等。而国内相关报道很少,只有北京航空材料研究院先进复合材料国防科技重点实验室等少数机构对APC-2/AS4热塑性预浸带进行了缠绕实验,并对制品性能进行了初步分析。可以说国内这种工艺还处在逐步开发的阶段,发展空间较大。伴随着国内高性能热塑性树脂的不断发展及其生产成本的降低,它必将逐步成为一种很有希望的复合材料成型工艺。