引言
众所周知,国内轮胎业外胎硫化定时控制仍较普遍地存在着以下问题:①使用机械式程序定时器,操作工可随意变更硫化时间;②由于用于硫化加热的过热水温度是变化的,这又要求操作工根据过热水温度变化的情况调整硫化时间,而实际上操作工为追求产量,往往缩短硫化时间,或对过热水温度的持续降低不给以足够的延时;③实际上人工确实很难确定很合适的硫化延时。因为即使根据经验规则来确定延长时间,也需要综合考虑过热水温度和模温在硫化中的整个变化过程以及轮胎本身的种种情况。对于这些问题,国内已做了大量的工作,目前已有不少轮胎厂采用可编程控制器(PC)或其它计算机控制设备来进行硫化定时控制,特别是采用PC已得到了普遍的肯定。但是由于普通PC其软件的局限性,对于根据过热水温度变化等因素而自动调整硫化定时这个关键问题(也即所谓的等效硫化控制问题)仍未能很好地解决。
从自动控制技术的角度看,轮胎自动定时硫化控制是个包含着温度(及/或压力)测量调节与时序逻辑控制的混合控制问题。为此我们采用了国产的擅长于混合控制的可混合编程的可编程控制器(以下简称HPC),获得了成功。HPC的主要特点是:可以来用其所提供的各种软件功能块与梯形图混合编程。因为梯形图擅长于处理逻辑量控制,而软件功能块擅长于模拟量控制。通过两种方式的混合编程,处理模拟量与逻辑量兼有且相互关联的混合控制问题就特别方便而PC具有可编程的数字显示和运行操作仪表面板,可以很方便地通过表格指定多个数据如温度、时间在运行中显示;HPC的核心硬件是功能很强的16位单片微机8098,因为8098片内带有A/D及D/A转换功能,所以HPC对模拟量控制的硬件成本就很低。
2 硫化自动定时的控制任务及硬件配置
2.1 控制任务
根据广州轮胎厂宝力公司的实际情况,确定HPC的控制任务如下。
(1)根据过热水温度的变化,自动对硫化时间进行调整。
(2)对硫化全过程进行时间顺序控制。
(3)测量并显示模温和过热水温度,其中原来接于三针记录仪的两个铂电阻改接于HPC,而由HPC把铂电阻测温信号经软件线性化处理后,以4~20mA标准电流信号传送给三针记录仪。
(4)对模温进行PID调节,HPC输出4~20mA的电流信号给电气转换器,进而操纵气动调节阀。
(5)对过热水温和模温进行监视,对超过规定时间的温度超限进行报警及逻辑处理。
这里需要说明的是,就HPC功能而言,所取的调节对象不一定是模温,也可以是蒸汽压力等。所配接的记录仪不必拘泥于三针记录仪,也可以是其它类型的记录仪,或者板式微型打印机,在使用多台HPC时,则可通过RS485通讯链路与个人计算机相连,进行高级的数据集中管理。
2.2 硬件配置
根据上述测控任务而配置的硬件包括:电源插件、主机插件、多动能输入输出插件,16点继电器输出插件和可编程数据显示器。多功能输入输出插件包括:
①模拟量输入2路铂电阻输入和2路标准电流/电压信号输入;
②模拟量输出:4路光隔,其中调节输出1路,温度记录输出2路,备用1路;
③开关量输入输出为直流光隔型,输入和输出各8点,用于按钮输入和状态提示灯输出。
16点继电器输出用于驱动7个双控电磁阀和2个外部联锁。
3 控制应用软件
针对上述控制任务而确定的软件功能块组态见图1,下面对图1作简单介绍。
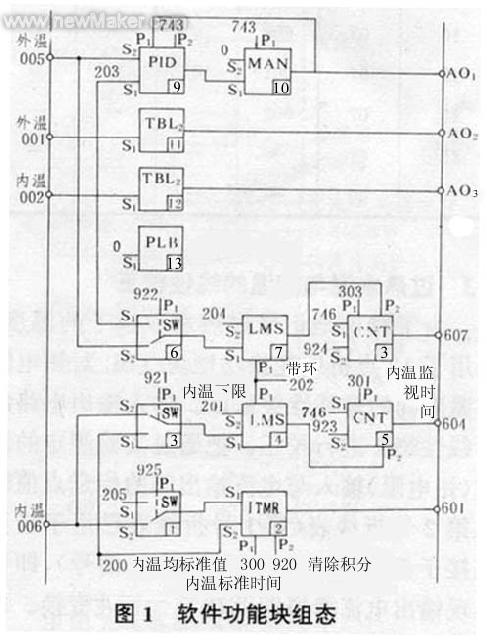
3.1 符号表示
整个应用软件组态采用了8种13个软件功能块。图中软件功能块形象地以方块表示,每一功能块与其它功能块的互连是通过赋予其端子S1、S2、P1、P2以信号代码来实现。HPC对包括每一功能块输出信号在内的各种内部外部信号都赋以唯一的信号代码,图中各功能块端子所标注的三位数字即是该端子所连信号的代码。功能块右下角标注的数字是该功能块运算的先后次序。图中左侧竖线表示输入信号界面,右侧竖线表示输出信号界面。为便于通过编程键盘输入,把图1用表1来表示。表中一行为一个功能块的登记项,共5项:包括功能块的编号,四个端子S1、S2、P1、P2所软连接的信号代码。未有定义的端子项下无须填信号代码,以符号“—”表示,也可填以数字“0”。各功能块填写的顺序与图1标注的顺序号一致。最后一行的功能块编号项下填以0,表示程序结束。因篇幅有限,其它表格如输入表、输出表、显示表、实数参数表、整数参数表、PID参数表等省略。
3.2 模温PID调节
图中PID调节功能块与MAN(手动操作)块相互连接构成了外温调节器。其中PID块的S2端软连接经过输入软件处理(由输入表指定)的模温输入信号005,经MAN块的输出软连接于模拟量输出端A01(由输出表格指定),接于PID块S1端的外温给定值由实参数表第4项203决定。PID块的其它参数在PID参数表中指定。
表1 软件功能块组态
运算符号 |
功能块编号 |
端子信号代码 |
S1 |
S2 |
P1 |
P2 |
1 |
12 |
205 |
006 |
925 |
0 |
2 |
10 |
600 |
200 |
300 |
920 |
3 |
12 |
200 |
006 |
921 |
0 |
4 |
13 |
602 |
201 |
202 |
0 |
5 |
11 |
746 |
923 |
301 |
603 |
6 |
12 |
203 |
005 |
922 |
0 |
7 |
13 |
605 |
204 |
202 |
0 |
8 |
11 |
746 |
924 |
303 |
606 |
9 |
02 |
203 |
005 |
609 |
743 |
10 |
03 |
608 |
0 |
743 |
0 |
11 |
07 |
001 |
0 |
0 |
0 |
12 |
07 |
002 |
- |
- |
- |
13 |
01 |
- |
- |
- |
- |
14 |
00 |
- |
- |
- |
- |
3.3 过热水温与模温的线性校正
为了精确地记录过热水和模子的温度,采用了12点折线变换功能块TBL对铂电阻与温度间的非线性关系以及输入输出电路的非线性统一进行校正。把通过实验测定的温度(铂电阻)输入与电流输出间的标定点值输入第2号折线表(第1号折线表己用于校正连接于PID块S2端的外温输入信号),即可实现输出电流与输入温度间的线性变换。由于两个温度通道的非线性一致,故在组态图上,2号折线块使用了两次,其输入分别接于信号001(模温)和002(过热水温),其输出分别软连接于模拟输出端子2(A02)和(A03),这由输出表格中指定。
3.4 温度超限监视
运算顺序号为3、4、5及6、7、8的功能块分别用于过热水温和模温的超限监视,其原理是相同的,现以功能块3、4、5为例来说明。当未进入硫化阶段时,由梯形逻辑产生的内部开关信号921为0FF(即0),开关功能块SW的输出为标准过热水温设定值,且大于低限监视功能块LMS的S2端所连的温度下限信号201(实参数表第2项),LMS的输出为0FF,则超限计时累加器CNT停止累加计数。当进入硫化后,信号921为0N,SW功能块的输出为过热水测量值006,只要006大于LMS块S2端的低限,LMS块的输出始终为0FF,CNT功能块为保持状态。一旦006低于201,则LMS输出为0N,CNT功能块对其S1端所连的秒脉冲信号746进行累加,只要累加的秒脉冲数小于其P1端子的超限时间预置信号301的值(整数参数表第2项),则CNT功能块输出为0FF,一旦高于此预置数,则输出信号604为ON。此信号在梯形逻辑中将点亮报警灯并对下一次硫化启动进行封锁。只有用外部确认按钮输入才能清除CNT并解除封锁。若CNT块输出为0FF,则当硫化阶段结束时.由梯形逻辑产生的信号923将把CNT复位清除。
3.5 自动定时
运算序号为1和2的功能块用于硫化时间的自动定时。迄今国内外对外胎硫化的实际过程已进行了大量的研究,由于硫化过程中传热与温度分布的动态过程很复杂,试图通过建立精确的数学模型来进行硫化控制至少在目前还不可能。见之于报导的成功的所谓等效硫化控制,其理论依据大多是各种积分关系式,这些积分关系式本质上仍是一种工程化的解析式,在具体实施时需要给出一些经验数据,而这些经验数据的确定,本身就很困难且往往附加有一定的限制条件。为了进一步简化问题,往往再做一些假设,以便把需要给出的经验数据减到最少,这样计算的结果偏离实际过程就更远了。但尽管如此,由这些简化的工程化的关系式计算的结果还是比人工操作好,通过凑试少量数据就能接近经验规则。因此从工程实用性看,简化的工程化的关系式是可以接受的。
我们所采用的计算硫化定时的工程化的关系式定义如下:
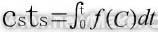
式中ts——工艺规定的硫化时间;
Cs——以正常的过热水温记录曲线上按矩形面积等效估计得到的平均标准过热水温;
f(C)——实际过热水温的函数。
由此式可见,等式左边表示工艺规定的或正常情况下应提供的硫化的热量,对实际温度C的函数变换f(C)经过一定时间的积分,当所积分的面积(热量)与式左边相等时,硫化即可结束。因篇幅所限,将另文详述这一关系并证明这一积分关系与文[4]所提及的阿累乌尼斯公式是一致的。按照这一关系,在使用非线性积分定时功能块ITMR时,需要设定3个参数:工艺给定的标准硫化时间ts;从记录曲线上按图2的虚线高度确定的平均标准过热水温度Cs以及从实际温度C变换到f(C)的一个变换系数。
在图1中,ITMR块的S1端为输入温度006,S2端为Cs值对应的信号200(实参数表第1项),P1端是ts对应的信号300(整数参数表第1项),变换系数填写在实参数表第3项(图中未注)。当积分值等于Csts,ITMR功能块的输出信号601为0N,对梯形逻辑部份进行了作用。
3.6 时间顺序控制
顺序号为13的PLB功能块是整个硫化时序梯形逻辑在功能块图上的表示。其具体内容是由约200句梯形图助记符语句组成的,通过编程键盘专门输入。此梯形逻辑通过内部信号920~925,601,604,607等与其它功能块进行联系,从而完成信号切换、越限超时报警、启动联锁、清除积分、延时控制等功能。因篇幅所限,图3中只画出梯形图中与功能块图有关联的部份,以便于读者了解梯形图与功能块之间如何相互作用。
由图3可见:
(1)当过热水温或模温其中之一超限超时,而使计数器CNT输出604或607为0N时,外部启动按钮信号800不起作用,必须由外部超限确认按钮按下而产生信号802,使923、924为ON,清除超限时间计数器CNT,使604、607为0FF后,启动信号800才能有效。若超限计数未到预置数,则604或607为0FF,在硫化阶段之后将依次使921、922为0FF,从而使923、924为0N,复位并清除超限计数器CNT。
(2)当进完一次水并进入硫化(进高压过热水)后,辅助继电器002为0N,003为0FF,开关功能块SW的切换信号921、922被置为0N,功能块方面开始过热水温与模温的超限监视。若过热水温未超限,603为0FF,925为0N,开始过热水温积分定时。按用户的工艺规程,在硫化过程中,若过热水温超限,因603为0N,则925为0FF,积分定时器输入为零信号205(实参数表第6项),这等效于停止积分,在此同时,过热水温超限计时开始进行。若过热水温在超限计时到达预置数之前又上升超过低限,则可又开始积分。在进过热水之前,002为0FF,011为0N,或在冷水循环结束之后,014为0N,这两种情况均使920为0N,从而使积分定时器复位。
(3)积分定时器输出信号601和硫化预置定时器触点501为串联,这是应用户的要求进行的连锁,以保证硫化时间不会少于工艺规定的硫化时间(即定时器501预置的定时时间),若取消定时器501,则硫化定时将完全由积分定时器决定。若硫化开始后过热水温越限计时到达预置数,CNT输出604为0N,则将短接601而取消积分定时。这种情况下,硫化定时仅由定时器501决定。在必要时还可启动一个手动延时(此部份逻辑未画出)。
(4)当积分定时到或温度监视计时到,将分别点亮标识灯421、422和423。 |
|